CNC Machining Service Manufacturer: A Comprehensive Guide
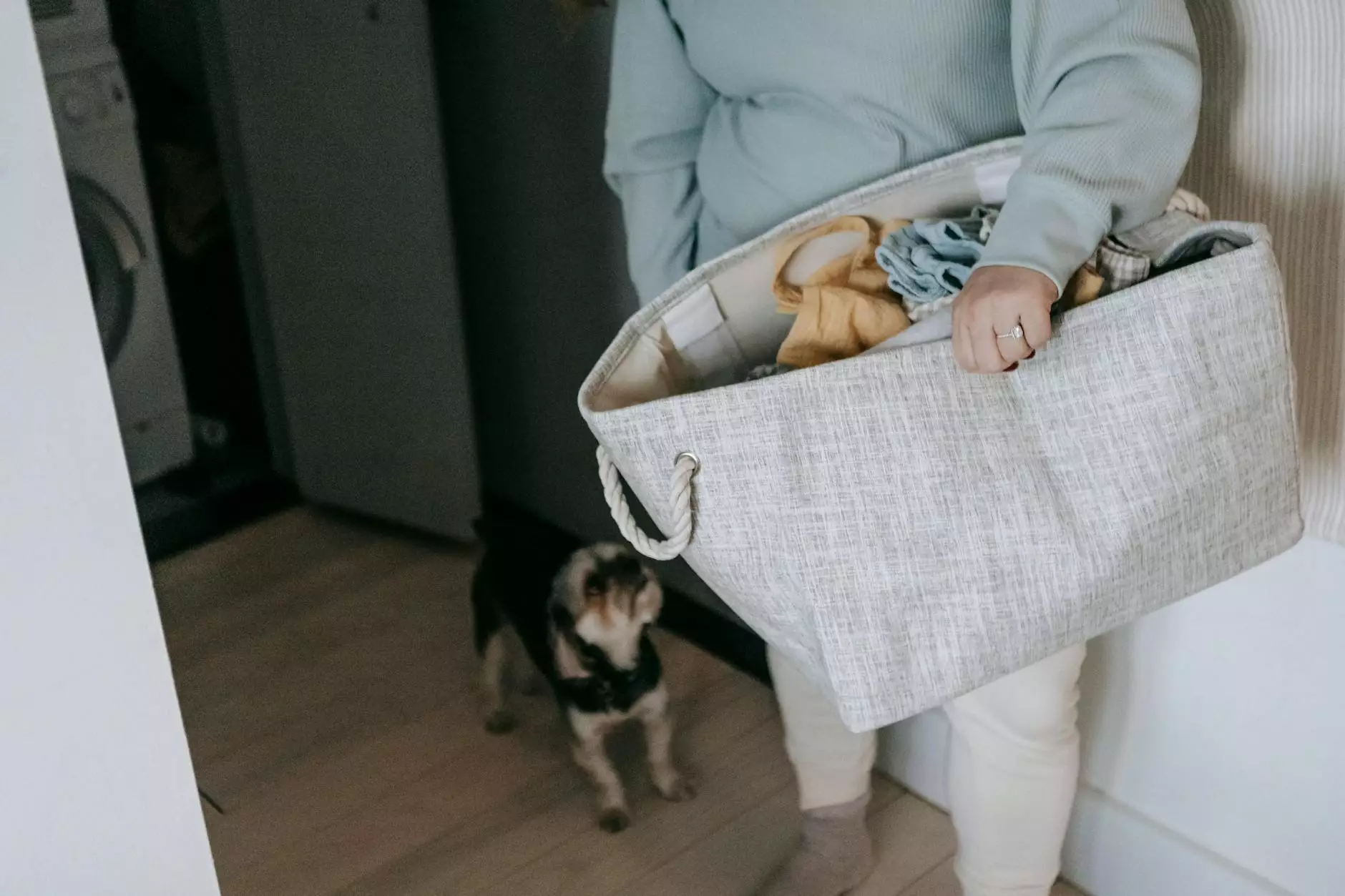
The world of manufacturing has gone through a tremendous transformation in recent years, with CNC machining at the forefront of these changes. As a leading cnc machining service manufacturer, we at DeepMould.net are dedicated to providing insights into this essential aspect of modern manufacturing. In this article, we will delve into what CNC machining entails, the benefits it offers, and why partnering with a specialized manufacturer is crucial for businesses across multiple sectors.
Understanding CNC Machining
CNC, or Computer Numerical Control, machining refers to the automated control of machining tools (such as drills, lathes, and mills) via a computer. This technology allows for precision manufacturing of parts and components used in a wide array of industries. Here are the fundamental aspects of CNC machining:
- Precision and Accuracy: CNC machining can produce intricate parts with tolerances as tight as ±0.001 inches.
- Flexibility: It can handle a vast range of materials, including metals, plastics, and composites.
- Efficiency: Automated processes significantly reduce labor costs and production time.
- Consistency: High repeatability makes it ideal for mass production.
The Importance of a CNC Machining Service Manufacturer
Choosing the right CNC machining service manufacturer is crucial for the success of your projects. The right partner can not only enhance the quality of your products but also streamline your supply chain. Here are several reasons why this choice is significant:
1. Expertise and Experience
Industry-leading manufacturers boast years of experience in CNC machining. Their knowledge in design, fabrication, and finishing processes ensures that your parts meet all specifications and industry standards. Partnering with an expert helps you avoid common pitfalls and enhances your project’s success rate.
2. Advanced Technology
Top-tier manufacturers invest in state-of-the-art equipment and software that allow for complex designs and faster turnaround times. The adoption of the latest CNC technology ensures that your parts are manufactured with the highest precision and efficiency.
3. Custom Solutions
Every project is unique. A quality cnc machining service manufacturer offers custom solutions tailored to your specific needs. This adaptability can significantly improve productivity and reduce waste.
4. Quality Assurance
Reputable manufacturers have stringent quality control processes in place. They employ various inspection methods to ensure that every part produced meets the highest standards of quality and reliability. This commitment to quality minimizes errors and defects in your final products.
The CNC Machining Process Explained
Understanding the CNC machining process can help businesses appreciate the complexity involved in manufacturing. Here’s a step-by-step breakdown:
Step 1: Design Creation
The process begins with creating a 3D model of the part to be manufactured. This can be done using CAD (Computer-Aided Design) software, which allows for intricate designs that can be simulated before production begins.
Step 2: Programming
Once the design is complete, a CNC programmer converts the CAD design into a machine-readable format called G-code. This code controls the movements of the CNC machine, detailing how the machine should move, cut, and shape the material.
Step 3: Material Selection
The choice of material is vital for ensuring the final product's performance. Common materials used in CNC machining include metals like aluminum, steel, brass, and various plastics. Each material has its own characteristics, which affect the machining process.
Step 4: Machining
During the machining phase, the material block is secured in the CNC machine. The machine then follows the programmed G-code, cutting away material to create the desired shape. This can involve various processes, such as milling, turning, or electrical discharge machining (EDM).
Step 5: Finishing
After the initial machining, the part may undergo further procedures like sanding, coating, or additional machining to achieve the required finish and tolerances. This step is vital for enhancing both aesthetics and functionality.
Materials Commonly Used in CNC Machining
Understanding the materials that can be utilized in CNC machining is essential for manufacturers. Here’s a list of common materials:
- Aluminum: Lightweight and versatile, making it ideal for various applications.
- Stainless Steel: Known for its high strength and resistance to corrosion.
- Brass: Offers excellent machinability and corrosion resistance, often used in electrical components.
- Plastics: Materials like ABS and Nylon are used for lightweight components requiring good wear resistance.
- Composites: Combining multiple materials, composites provide enhanced performance in specific applications.
Industries That Benefit from CNC Machining Services
The applications of CNC machining are vast, cutting across numerous industries. Here’s how different sectors utilize these services:
Aerospace
In the aerospace industry, precision is paramount. CNC machining services produce critical components like turbine blades and structural parts, ensuring high strength-to-weight ratios and adhering to strict regulatory standards.
Automotive
The automotive sector frequently employs CNC machining for the production of engine components, transmission parts, and custom fittings. The speed and efficiency of CNC technology enable manufacturers to keep pace with rapidly changing market demands.
Medical Devices
In medical device manufacturing, CNC machining is utilized to create intricate parts with high tolerances, such as surgical instruments and implants. The ability to produce sterile and customized components is critical in this field.
Electronics
For the electronics industry, precision components are essential. CNC machining helps in manufacturing housings, brackets, and other parts needed for devices ranging from smartphones to industrial machinery.
Defense
The defense industry relies on CNC machining for robust and reliable components that can withstand extreme conditions. These can include weapon systems, surveillance equipment, and vehicles.
Benefits of Partnering with a Reliable CNC Machining Service Manufacturer
By collaborating with a trustworthy cnc machining service manufacturer, businesses can leverage a multitude of advantages, such as:
- Cost Savings: Outsourcing machining services can drastically reduce production costs and overhead.
- Faster Turnaround: Manufacturers can offer shorter lead times thanks to their streamlined processes and advanced machinery.
- Scalability: CNC machining services enable businesses to scale production up or down based on demand without excessive investment in equipment.
- Focus on Core Competencies: By outsourcing CNC machining, companies can concentrate on their core business functions while leaving precise manufacturing to experts.
Conclusion
The landscape of manufacturing is continuously evolving, and CNC machining plays a vital role in this transformation. As a reliable cnc machining service manufacturer, DeepMould.net understands the importance of precision, quality, and efficiency in the machining process. By partnering with a skilled manufacturer, businesses can ensure they are equipped to meet current challenges while remaining competitive in their respective markets.
In summary, whether you operate in the aerospace, automotive, medical, or any other industry that relies on precision manufacturing, choosing the right CNC machining service manufacturer can create significant value for your business. The investment in quality machining services not only enhances product quality but also contributes to your overall operational efficiency.