Precision Plastic Injection Molding: A Key Player in Modern Metal Fabrication
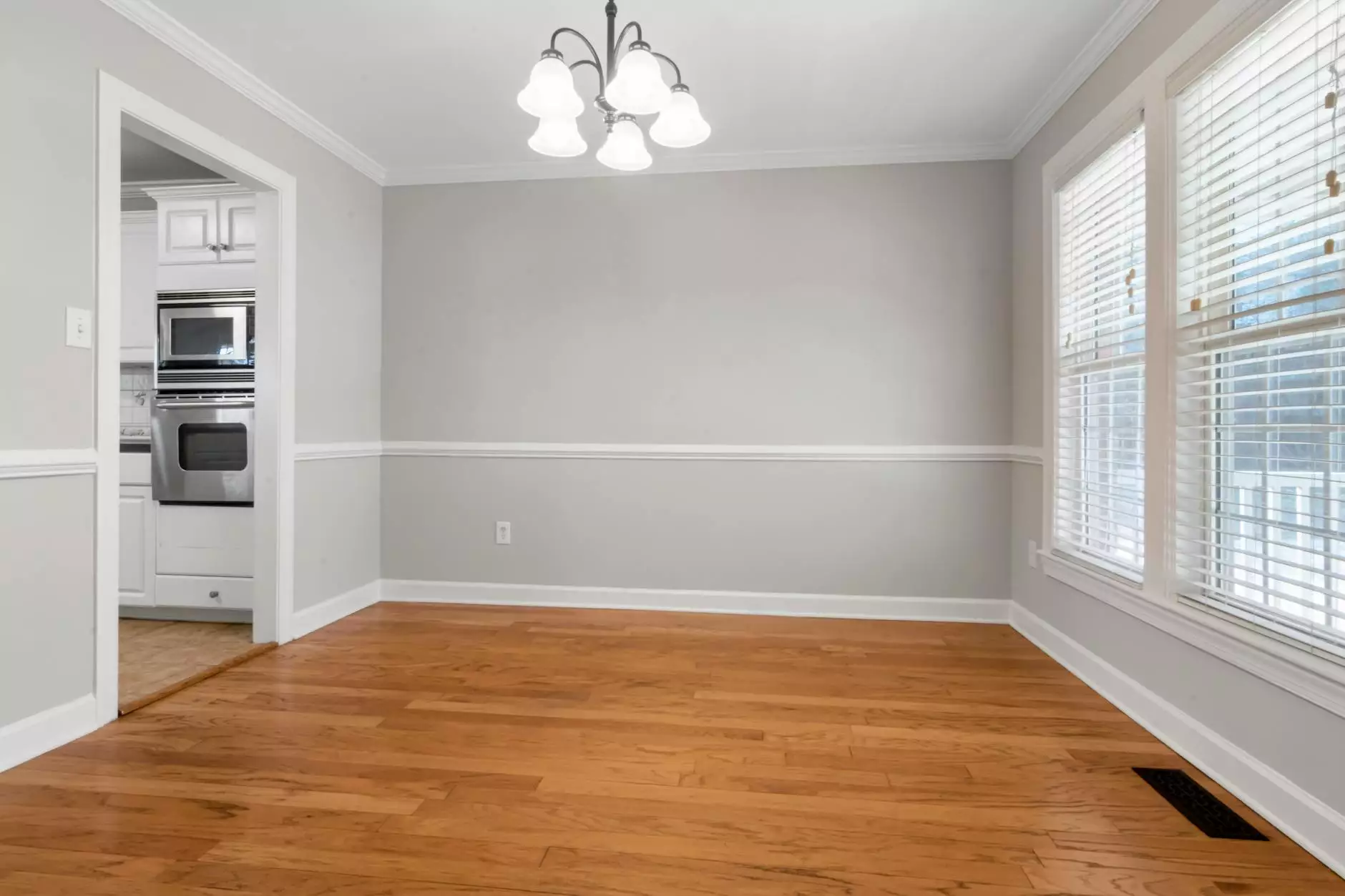
Precision plastic injection molding has emerged as a cornerstone of modern manufacturing, especially within the realm of metal fabrication. As industries progressively seek efficiency and quality in production processes, the integration of this technology stands out for its ability to deliver robust, high-quality components with remarkable accuracy. Understanding the intricacies of precision plastic injection molding is essential for companies aiming to enhance their manufacturing capabilities.
What is Precision Plastic Injection Molding?
The term precision plastic injection molding refers to a manufacturing process used to create parts by injecting molten plastic into a mold. This innovative approach enables the production of complex shapes and designs with precise tolerances and minimal waste. The advantages offered by this molding method have made it indispensable in various industries, including automotive, medical, and consumer goods.
How Precision Plastic Injection Molding Works
The methodology behind precision plastic injection molding encompasses several critical steps:
- Mold Design: The process begins with designing a mold that will shape the final product. Advanced CAD software plays a vital role in this phase, allowing engineers to create intricate designs that meet specific requirements.
- Material Selection: Selecting the correct plastic material is crucial. Factors such as strength, flexibility, temperature resistance, and finish are considered to ensure the final product meets the required specifications.
- Injection: Once the mold is prepared and the material chosen, the plastic is heated until it becomes molten. This liquid plastic is then injected into the mold under high pressure, allowing it to fill every cavity and detail.
- Cooling: After injection, the mold is cooled, which solidifies the plastic into its final shape. This cooling phase is critical, as it affects the strength and dimensional stability of the part.
- Mold Removal: Once the part has cooled and solidified, the mold opens, and the finished plastic part is ejected.
- Finishing Touches: Additional processes such as trimming, painting, or surface finishing may be applied to achieve the desired final product characteristics.
Key Benefits of Precision Plastic Injection Molding
Companies are increasingly turning to precision plastic injection molding for several reasons:
- High Efficiency: Injection molding is known for its rapid production capabilities, enabling manufacturers to produce large quantities of parts in a short time frame.
- Cost-Effectiveness: Although the initial setup cost for molds can be high, the per-unit cost drops significantly as production volume increases. This makes injection molding an economically viable option for many businesses.
- Design Flexibility: The precision of the molding process allows for intricate designs that can accommodate various functional requirements, making it adaptable to different applications.
- Consistency and Quality: This method ensures uniform quality and dimensional accuracy across all produced parts, minimizing the risk of defects and rework.
- Material Versatility: A wide range of plastic materials can be utilized, each offering unique properties that can be tailored to specific applications.
Applications Across Industries
The application of precision plastic injection molding spans numerous industries, showcasing its versatility and reliability:
Automotive Industry
In the automotive sector, manufacturers leverage this technology to produce parts such as dashboards, housings, and various electronic components. The need for lightweight yet durable materials makes precision injection molding an ideal choice.
Medical Sector
The medical industry benefits immensely from precision plastic injection molding as it allows for the production of sterile, high-precision medical devices and components. Items such as syringes, surgical instruments, and drug delivery systems are mass-produced with exact tolerances to ensure safety and efficacy.
Consumer Goods
From toys to household appliances, the consumer goods industry relies on this molding technique to create aesthetically pleasing and functional products efficiently. The ability to customize designs and colors further enhances product appeal.
Electronics
Precision plastic injection molding is crucial for the electronics industry, where components need to be safe, lightweight, and accurately manufactured. Items like connectors, casings, and other intricate parts are produced using this method, ensuring compatibility and performance.
The Role of Technology in Molding Process
Advancements in technology have significantly improved the efficiency and accuracy of precision plastic injection molding:
- 3D Printing for Prototyping: Before manufacturing molds, companies often use 3D printing to create prototypes. This allows for testing and modifications, saving both time and money.
- Computer Numerical Control (CNC): CNC technology assists in creating molds with high precision, ensuring that parts are produced accurately and consistently over time.
- Automation: Automated injection molding machines can operate continuously with minimal human intervention, drastically increasing production rates and reducing labor costs.
- Simulation Software: Companies use simulation tools to predict and analyze the injection molding process, optimizing molding conditions and material use while mitigating potential issues.
Challenges in Precision Plastic Injection Molding
Despite the numerous advantages, there are challenges that manufacturers must navigate:
- Initial Setup Cost: The investment to create high-quality molds can be substantial. However, this cost is often justified by the efficiency of mass production.
- Material Limitations: Not all plastics are suitable for injection molding. Understanding the properties of each material is essential to ensure it meets the specific requirements of the application.
- Maintenance of Equipment: Continuous use of injection molding machines requires regular maintenance to avoid breakdowns or decreases in quality.
- Environmental Concerns: The impact of plastic waste can be significant. Manufacturers are increasingly focusing on recycling and using biodegradable plastics to mitigate this effect.
The Future of Precision Plastic Injection Molding
The landscape of precision plastic injection molding is evolving. With growing emphasis on sustainability and efficiency, the industry is innovating at an unprecedented pace:
- Eco-friendly Materials: The development of biodegradable and recyclable plastics is on the rise, providing environmentally conscious options for manufacturers. This shift not only meets regulatory requirements but also appeals to consumers.
- Smart Manufacturing: The incorporation of IoT technology in injection molding machines allows for real-time monitoring of the production process, enhancing quality control and reducing downtime.
- Global Collaboration: As companies expand their operations globally, collaborative manufacturing networks are becoming more prevalent, leveraging regional expertise and technologies to optimize the design and production processes.
Conclusion
In summary, precision plastic injection molding represents a transformative technology in the metal fabrication industry and beyond. Its ability to produce complex, high-quality parts quickly and cost-effectively is a significant asset for manufacturers. As we move towards a future focused on sustainability and innovation, embracing this molding technology is essential for maintaining competitiveness in an ever-evolving marketplace.
For companies looking to integrate precision plastic injection molding into their manufacturing processes, Deep Mould offers unparalleled expertise and comprehensive solutions that can help streamline production and enhance product quality, setting a new standard in the world of manufacturing.