High Pressure Die Casting Mold: Revolutionizing Metal Fabrication
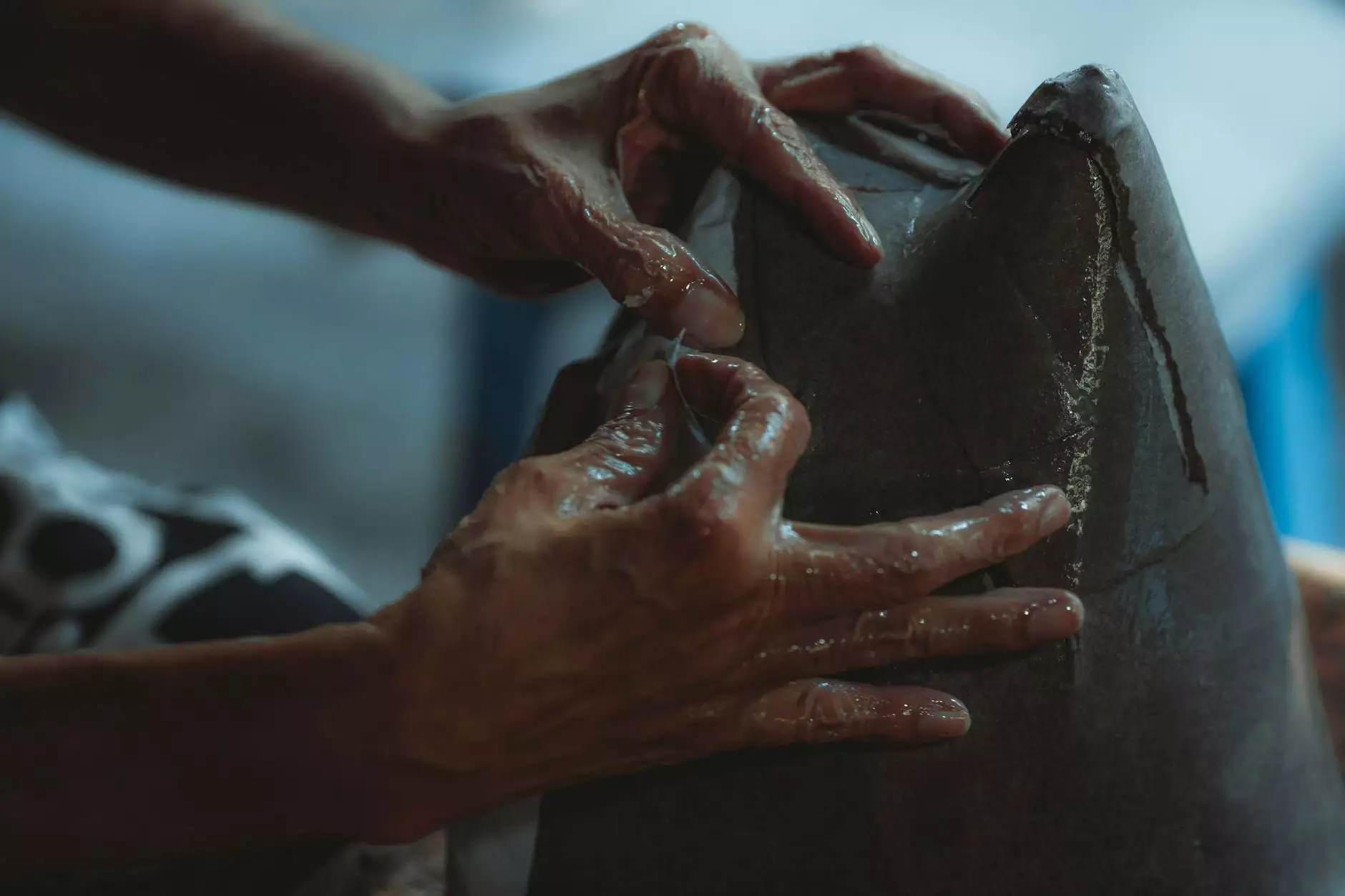
In the ever-evolving world of manufacturing, metal fabrication continues to be a cornerstone of industrial production, with advanced techniques and technologies at the forefront. Among these advancements, the high pressure die casting mold stands out as a game-changer, facilitating the creation of complex metal parts with precision and efficiency. This article explores the profound impact of high pressure die casting molds in the realm of metal fabrication, their applications, advantages, and the future they hold for the industry.
Understanding High Pressure Die Casting
High pressure die casting is a metal casting process that involves forcing molten metal into a mold cavity at high pressure. The process is characterized by its ability to produce highly detailed parts with excellent surface finishes and tight tolerances. The foundation of this process is the high pressure die casting mold, meticulously designed to withstand the intense conditions involved in the casting process.
How High Pressure Die Casting Works
The high pressure die casting process consists of several critical steps:
- Preparation: The die, made from materials such as steel or iron, is preheated to the optimal temperature to facilitate the flow of molten metal and enhance the quality of the cast.
- Molten Metal Injection: Molten metal is injected into the mold under high pressure, ensuring that it fills every cavity and detail of the mold.
- Cooling and Solidification: The metal cools and solidifies rapidly within the mold, taking on its final shape.
- Demolding: After a specified cooling period, the mold is opened, and the finished part is ejected.
- Finishing Touches: Depending on the application, further machining or finishing processes may be applied to meet specific requirements.
Key Benefits of Using High Pressure Die Casting Molds
The use of high pressure die casting molds offers numerous benefits, making them an attractive choice for numerous industries:
- Precision and Accuracy: The high pressure involved in the casting process ensures that complex shapes and intricate details are replicated accurately, resulting in high-quality parts.
- Efficiency: The rapid production cycle leads to a significant increase in throughput compared to traditional methods, reducing lead times and lowering production costs.
- Material Versatility: A wide range of metals can be used in high pressure die casting, including aluminum, zinc, and magnesium, offering flexibility to manufacturers.
- Durability: Parts produced through this method exhibit high strength and wear resistance, making them suitable for demanding applications.
- Reduced Waste: The process minimizes scrap production, as leftover metal can often be reused, contributing to sustainability efforts within the industry.
Applications of High Pressure Die Casting Molds
High pressure die casting molds are widely utilized across various industries, each benefiting from their unique attributes:
Automotive Industry
The automotive sector leverages high pressure die casting molds to manufacture components such as engine blocks, transmission cases, and chassis parts.
With the demand for lightweight and fuel-efficient vehicles rising, casting aluminum parts has become increasingly common, leading to improved performance and efficiency.
Electronics
In the electronics industry, the high precision provided by high pressure die casting molds is crucial for producing intricate housing and structural parts for devices such as smartphones, laptops, and other consumer electronics.
Household Appliances
From kitchen appliances to home fixtures, the durability and aesthetic appeal of die-cast components have made them ideal for various household products, enhancing both functionality and design.
The Future of High Pressure Die Casting Molds
As technology progresses, the future of high pressure die casting molds appears promising and full of potential:
Innovations in Mold Design
With advancements in computer-aided design (CAD) and simulation tools, manufacturers can now create more complex mold geometries than ever before. Innovations such as 3D printing of molds are also emerging, enabling rapid prototyping and faster iterations during the design phase.
Improved Material Technologies
The development of advanced materials will allow high pressure die casting molds to withstand higher operational pressures and temperatures, further expanding their application range. Additionally, the rise of smart materials may lead to self-healing molds or those that can adjust to varying operational conditions.
Sustainability Initiatives
As industries move towards greener practices, the recycling and sustainability of mold materials are gaining attention. Efforts to create eco-friendly alloys and processes that reduce energy consumption will be integral to the future of high pressure die casting molds.
Choosing the Right High Pressure Die Casting Mold Provider
When selecting a provider for high pressure die casting molds, consider the following factors:
- Experience and Expertise: Look for a company with extensive knowledge and experience in the industry.
- Customization Capabilities: The ability to design molds tailored to your specific needs is essential.
- Quality Assurance: Ensure the provider has rigorous quality control measures in place to guarantee the integrity and precision of the molds.
- Availability of Support Services: Consider providers that offer ongoing support, including maintenance and repair services for molds.
Conclusion
The high pressure die casting mold represents a significant advancement in the field of metal fabrication. By providing unmatched precision, efficiency, and versatility, these molds have become an essential component in various industries, from automotive to electronics and beyond. As the industry continues to innovate and adapt to new challenges, the potential for high pressure die casting molds to redefine manufacturing processes is immense. By understanding the intricacies and benefits of high pressure die casting molds, manufacturers can harness their capabilities to drive productivity and product quality to new heights.
For businesses looking to move forward in a competitive landscape, investing in high pressure die casting molds is not merely an option; it is a necessity for success. Choose wisely and embrace the future of manufacturing today.